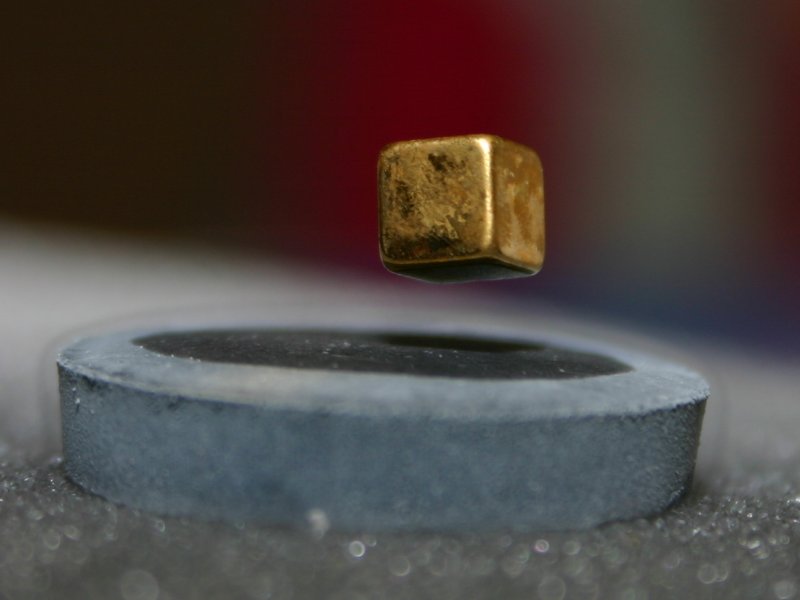
Fini le recyclage global dans le même bain de matière en fusion pour fabriquer de nouveaux aimants de mauvaise qualité. L’intégration raisonnée d’une certaine quantité d’aimants recyclés dans les futures productions d’aimants s’annonce prometteuse. Une équipe du Laboratoire d’innovation pour les technologies des énergies nouvelles et les nanomatéri
aux (LITEN) du CEA de Grenoble a démontré qu’il est possible de produire des aimants présentant des performances comparables à ceux du commerce en utilisant jusqu’à 30 % de matière recyclée.
La technique en cours d’amélioration permet un recyclage efficace d’un matériau largement utilisé dans les éoliennes. Les aimants riches en terres rares (néodyme et dysprosium) sont des matériaux stratégiques dont la consommation ne cesse d’augmenter en électronique et dans la production d’énergie renouvelable.
Le projet franco-allemand rassemble le CEA, l’Institut Fraunhofer et des industriels pour couvrir l’ensemble de la chaîne de valeur. Objectif : repérer et améliorer les points clés du recyclage pour diminuer l’oxydation des matériaux durant le processus. Les Terres Rares sont friandes d’oxygène et forment facilement des oxydes lors de leur mise en forme, même sous atmosphère inerte. Entre la récupération de l’aimant et son intégration, l’équipe pluridisciplinaire réussit à garder une concentration de 1 000 ppm d’oxygène. Un pourcentage proche des quantités contenues dans les aimants neufs permettant une intégration.
Pour cela le recyclage par voie sèche a été utilisé. Il consiste à broyer les aimants usagés (ou les rebuts de fabrication) et à réinjecter la poudre obtenue dans le procédé standard. Avec une poudre homogène (grains de 5 microns en moyenne) mélangée en différentes proportions avec de la poudre neuve, les chercheurs obtiennent après frittage une densification complète et des propriétés magnétiques presque équivalentes (moins de 3 % de perte) à celles d’un aimant fabriqué à partir de poudre neuve, et ce avec un quart de poudre recyclée.
Le laboratoire développe également deux autres procédés, par fusion ou par extraction chimique.
La fusion ne nécessite pas de connaître la composition exacte des aimants de départ ce qui l’avantage face au boyage. L’oxydation faible, proche de 1 000 ppm, est également plus facile à préserver. La composition est déduite à la sortie du four. Selon les concentrations en néodyme et dysprosium demandées, les lingots sont alors intégrés dans le bain de fusion qui produira les nouveaux aimants avec un taux d’insertion de 10 à 30 %. Cette technique est adapté pour les aimants de grosse taille comme ceux utilisés dans les éoliennes.
Pour les aimants plus petits, l’extraction chimique est mieux adaptée. En effet la gaine est souvent plus importante que l’aimant et un broyage serait contre-productif. Un bain d’acide est alors utilisé et selon le produit voulu, les terres rares sont précipitées sous forme de sels. Un procédé intéressant valable uniquement avec des aimants contenant plus de 30 % de terres rares.
Voir l’article de Baptiste Cessieux sur Industrie&Technologie à ce sujet